Understanding NADCAP
TABLE OF CONTENTS
A COMPREHENSIVE GUIDE
Lynn Welding offers NADCAP-approved welding services for numerous aerospace primes. Our team consists of 16 NADCAP-certified welders and 18 NADCAP-certified resistance spot welding machines. We have a stellar reputation within the aerospace community and are recognized for being the most responsive and transparent aerospace welding company. Our detailed guide provides an in-depth look at the NADCAP certification process, its significance, and the NADCAP-accredited services we provide.
INTRODUCTION
Lynn’s route to excellence and superior standards lies in its continuous dedication to maintaining its various accreditations. Arguably the most impactful on the company’s operational system and work culture is that of audits such as Nadcap.
The roots of Nadcap and Lynn Welding are considerably similar in makeup. From its origins as a one-man welding shop to a booming business, notorious for its exemplary services and dedication to fulfilling each customers’ goals as if it were their own, Lynn perhaps knows better than most just how remarkable the creation of the Nadcap audit has been. What started as a simple concept originating in an Equal Partners Conference and was later introduced as an acronym, has since established itself as a brand that no one in the aerospace industry can afford to ignore. Thanks to the combined efforts of Original Equipment Manufacturers (OEMs or primes), such as Pratt and Whitney, Northrop Grumman and GE Aviation, it is nearly impossible in 2021 to become an aerospace supplier without being Nadcap accredited.
Nadcap is an unprecedented development in the aerospace industry. Before its creation, it was unheard of that such a foundational institution would come into existence – and continue to be implemented – through the cooperation of industry experts, program subscribers, and providers.
Through the Performance Review Institute (PRI)’s continuous efforts – such as putting together meetings and activities for the Supplier Support Committee (SSC), Task Group, and Primes – Nadcap has been able to mutually benefit both the subscribers and their providers, while simultaneously driving aerospace standards and expectations of service with an audit that strives for continuous improvements within its field.
Lynn Welding utilizes the stringent checklists provided by the Nadcap audit in conjunction with that of AS9100, another global aerospace standard, as a meter stick to prompt itself to continually grow and adapt into a bigger and better company – not only to become a place worth working for, but also to work with. With a long list of accreditations under its belt and over 60 years of experience, Lynn holds itself to extremely high service standards.
To maintain its eminence in the aerospace, military, medical, and defense industries, Lynn is always looking to implement better ways of handling, producing, and distributing products. In our typical, good-natured spirit of things, we have decided to put together this comprehensive guide to Nadcap and all it entails in relation with our special processes so that others might also come to understand the depth of its continued impact on the aerospace and defense industries.
Keeping aircraft production at peak levels while continuing a track record for safety means the need for reliability and quality manufacturing. Aerospace vendors must produce safe and efficient airplanes while simultaneously seeking new technology and equipment to drive the industry forward. Doing so requires significant involvement at all phases within the supply chain, especially with specific aircraft under scrutiny due to 2019’s crashes.
Programs such as Nadcap were designed to perform audits and provide the necessary accreditation for aerospace manufacturers. By taking the time to educate yourself on the Nadcap program, you will understand how suppliers and manufacturers partner together to improve efficiency and safety across the aerospace industry.
.png?width=300&name=Untitled%20design%20(76).png)
THE PERFORMANCE REVIEW INSTITUTE
The company responsible for administering the Nadcap audit is the Performance Review Institute (PRI).
PRI was created through the concerted effort of aerospace Original Equipment Manufacturers (OEMs or primes). Throughout its development, it has sought to be an instrumental mediator between the needs of primes and their suppliers. Subscribers are audited by PRI as well, with the hopes of managing and ensuring the quality of the systems in place at every level of an aerospace job.
There are several tiers to the internal organization of PRI to ensure that the audits never overstep their bounds or trample on the needs or concerns of the suppliers. The key department in this effort is the Supplier Support Committee (SSC), through regular meeting and discussions, the committees garner the general opinion and input of suppliers. Nadcap is an audit with a core concept of being mutually beneficial to every tier that it’s applied to in the industry, whether one is a prime, a tier one supplier, or tier two. Therefore, the activities brought up during committee gatherings and events are intentionally designed and implemented to keep enhancing and improving the effectiveness of the audit at meeting the needs of suppliers and subscribers.
Members of the Task Groups department are also in attendance at SSC events. The Task Groups are the people in charge of choosing expert engineers from the specific field of a given company to audit them. For instance, only welding experts can proctor an audit to a welding company, so the Task Group would be the ones in charge of finding a reliable, knowledgeable auditor for them. To become a Nadcap auditor is an entirely different series of procedures from what suppliers like Lynn Welding have to go through during a Nadcap audit.
The managerial sub-departments within the PRI include: the board of directors, administrative staff, and the Nadcap Management Council (NMC). All of which are responsible for ensuring that any issues occurring at the level of the Task Groups and SSC’s are properly and completely managed.
PRI is a not-for-profit, industry-driven company. Through their dedication to making Nadcap better and better each and every year, the audit has become one that represents consistency, high standards, and control. For every question on the audit’s checklist, there are a hundred different controls that could, and often are, double-checked and verified.
WHAT IT MEANS TO BE NADCAP ACCREDITTED
Aerospace has some of the most comprehensive and stringent regulations out of any other industry. When it comes to ensuring the safety of civilians, it is vital that every process and product involved in the creation of an aircraft is maintained within tight tolerances and without flaws. Without strict management, there would be virtually no assurance that the plane, jet, helicopter, etc. taking off will be able to maintain its flight.
Nadcap, in turn, has become that assurance. The role of welding companies in this industry is especially crucial to a project’s success or failure; they are quite literally the glue holding the aerospace industry together. The primes and subscribers look for this accreditation before approaching new welding suppliers, as it shows that they have a documented and proven dedication to excellence.
In pursuance of Nadcap accreditation, suppliers must show that their processes are compliant and well-established. When a PRI industry-approved auditor comes to the facility, it is within their rights to ask technical questions of any employee on the premises. Therefore, it is important that a new welding company takes the time to reflect on and implement the changes necessary to fulfill Nadcap’s requirements. The accreditation process is not a one-day pass or fail test, nor is it a multiple-choice quiz that employees can study for the night before and expect to pass.
It is well-known in the industry that obtaining a Nadcap accreditation is directly connected to a company’s attention to detail and dedication to excellence. In order to pass an audit administered by PRI, you really have to pass 3 audits – one internal, one from the appointed expert, and the follow up review from the members of the Task Group.
The assignment of internal auditors is especially important during the preparation phase. The Nadcap audit is a fluid assessment of any given special process. An auditor that comes to the facility can ask any procedural question they feel necessary, so long as its within the pre-determined scope of the audit. This means that in order to pass, one really has to already have a solid understanding of: 1) where they’re starting, 2) what they could improve on, and 3) how to best alter course to keep up with the forever expanding and improving scope of the audit. Through the practice of keeping designated internal auditors, welding companies will be better equipped to prepare for and surpass the expectations of the upcoming audit, as well as keep pace for future ones. There is little that goes unchecked by auditors, and each one has their own method of getting things done. A proper internal audit’s purpose then is to prepare and troubleshoot as much as possible before the auditor gets there.
Internal audits will point out their own flaws, drop-offs, or opportunities for improvements in the special processes that the Nadcap audit will later go through with a fine-toothed comb.
In order to feel secure in the face of the upcoming audit, it is necessary that internal audits are placed on the same level of importance as the official one. An unprepared company is going to fail. To not fall within that category, internal auditors are an indispensable investment that every aerospace company should regard as essential.
Here at Lynn Welding, we are constantly looking for ways to better our system and prepare for the ever-evolving Nadcap audits. Our internal auditors, therefore, are encouraged and supported in their efforts to continuously learn and stay up to date on the latest quality systems, seminars, and trainings.
The Nadcap audit covers everything from scotch brite containment to certifying the legitimacy of weld schedules. Lynn Welding performs three primary special processes to the aerospace industry that serve as categories for the auditor to divide their evaluations into – fusion welding, resistance welding, and torch brazing. Depending on which prime a company works with, there may also be additional requirements and parameters that need to be documented. This is all in an effort to make Nadcap as widely applicable in the industry, while staying centralized and focused on key areas, as possible. One of the primary goals of this audit is, after all, to negate the need for frequent or recurring audits from customers.
Nadcap accreditation depends on a company’s ability to prove that their processes are controlled, repeatable, and meet industry and customer specific standards every time. It is not enough to simply state that you perform any given task, there has to be qualifying objective evidence to support most every statement made during an audit.
What this means for welding companies in particular is that primes and their direct suppliers can feel secure in relying on the Nadcap audit as a means of evaluating compliance. Rather than being routinely audited by these aerospace companies – which often leads to overlap and various redundances – time and money on both sides are saved by Nadcap evolving to reflect the ever-developing requirements of the industry. Thereby, the audit is able to maintain its status as the most reliable means of evaluating any facility to the full extent of the total scope of the aerospace work it’s responsible for.
Passing a Nadcap audit proves to potential, and existing, customers that your facility’s procedures, certifications, and personnel can withstand strenuous and thorough scrutiny. Through the dual-accreditation of Nadcap and AS9100 – an international standard that looks at the managerial system rather than special processes – Lynn Welding demonstrates that they are a well-established and reputable supplier at every step of the process.
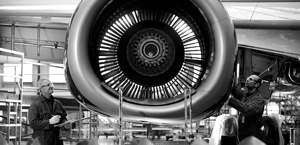
PROCESS OF NADCAP ACCREDITATION
The route to becoming Nadcap accredited is the same for any supplier. As previously stated, it is recommended that companies aim for a scheduled integration of Nadcap compliant systems through a yearlong planning process. There are a number of guides already readily available on the internet to assist with such an undertaking, so it won’t be re-hashed here, and instead this section will detail the process as if the yearlong preparations have already been properly attended and addressed.
When the company has completed their preparations and has passed their own internal audit, ensuring that they are ready for the actual Nadcap proctor to visit the facility, then they will have to request an official audit from the PRI website. They will then be contacted to finalize the schedule, and an expert in their field will be assigned to them. Unlike AS9100, where the auditor is responsible for that company for five years, the assigned one for Nadcap is not guaranteed to be the same and is likely to change each time. If the auditor does not get along with, or has problems/conflict, with their assigned location, then it is also within that company’s rights to request a new auditor be chosen.
The duration of the audit depends on the size of the company, and the projected timespan is typically conveyed long before the auditor arrives. For the length of the audit, the proctor will hold daily debriefing meetings to discuss any new findings and general progress updates.
It is important that any questions or disputes are brought up and discussed during this time, well before the audit is completed and submitted to the Technical Staff for review
Throughout the duration of the audit, there are a number of ways a given auditor may choose to organize or schedule things, but there are a few aspects of Nadcap that are guaranteed to take place. With each service that needs to be verified and gone through, the auditor performs three primary tasks: going through the accompanying checklist – which will be previously supplied so that they can be filled in and submitted 30 days beforehand – reviewing the paperwork of accompanying jobs chosen, and personally viewing work on the floor. The checklists vary every year the audit takes place, so the only real way to be fully prepared is to stringently adhere to a yearlong preparation schedule and have a thorough internal audit take place prior to the official PRI one.
To ensure that only the questions that apply to any given company are assessed, the auditor will ask the quality team to review the scope before any processes can begin being evaluated. Once the scope has been signed off on, it cannot be modified or argued against. For this reason, it is extremely important that these initial steps are carried out by a fully competent and informed member of the staff. Perhaps to ensure that this is already the case, in order to hold a Nadcap audit, a company must already have a qualified quality system. In Lynn Welding’s case, our quality department is currently kept to AS9100 compliance requirements.
To ensure that a Nadcap audit is effective, it has to be thorough; therefore it is vital that no time is unnecessarily wasted. To this end, not having pre-submitted and filled out all of the checklists is a minor finding and can possibly even lead to additional charges being brought up against the company for.
After the auditor finalizes the records online, the PRI Technical Staff are the ones who initially receive and review the company’s results, as well as approves any root cause corrective actions. Corrective action reports (CARs) are the resulting plans of action for any major or minor findings resulting from the audit. It is not unheard of that a CAR is rejected on the first try, so it is especially important that first time audit participants take their submissions seriously, as the deadline to submit corrections is extremely restrictive after the initial one. On-site corrective actions can be accepted by the auditor, but they are essentially just a first-time submission. The finding will remain open until the supplier uploads all of their corrective actions, and the on-site approval will then be reviewed alongside the other submissions by the Technical Staff.
After the close of an audit, there is a twenty-one-day deadline to submit root cause corrective actions. Determining a root cause for findings that have been grouped all together and reported as one minor NCR is vital in maintaining merit status and keeping the number of findings to a minimum. If the Technical Staff does not agree with the root cause supplied by the quality team, then they may choose to no longer accept them as one group and instead split them off into separate findings altogether.
There are five standard headings that come pre-populated when submitting a corrective action report (CAR) through the PRI portal: immediate containment, root cause, impact of identified cause, action to prevent, objective evidence, and effectivity date. The Staff Engineer has 14 days after the submission of the above necessary information to provide their pass or reject verdict. If the Staff Engineer rejects the CARs submitted, then the quality team has a deadline of 7 days before they have to resubmit a second, updated version addressing what the Staff Engineer has designated as unsuitable or insufficient. The new submission has to be responded to within 7 days by the Task Group.
A company can only submit a corrective action 3 times. After the third failure, there are two potential outcomes: 1) the company fails their Nadcap audit or 2) they are granted another chance. The route taken is up to the Staff Engineer to forward along to the Task Group to reject or accept. If a company fails the audit, then they will need to put out a statement to all their customers informing them that they have failed the audit, and modify all of their products, services, and documents to no longer contain anything to have to do with Nadcap (if they are a previously established Nadcap accredited supplier, that is).
The loss of Nadcap accreditation is therefore very damaging for a company. Not only are your findings published on your virtual record – this happens regardless of whether you pass or fail – but now your loss of status has been broadcasted to all of your current and potential customers.
To attain a Nadcap accreditation is to proclaim that your procedures and products are stringently maintained and measured to the highest of standards. To lose a Nadcap accreditation is therefore announcing the very opposite. Your customers will think you are sloppy, unreliable, and negligent in maintaining and managing your internal systems. There would be a significant loss to the business.
However, if we assume that the Task Group has approved the audit and corrective actions, then the company will be accredited as Nadcap approved to service the aerospace industry. This approval comes with the ability to use the Nadcap logo and name, which is likely to also attract more subscribers and customers into utilizing your business.
For Lynn Welding, this accreditation is especially vital for our business, because we provide services to the leading primes of the aerospace industry, as well as a number of military and defense ones. Our customers are especially reliant on our Nadcap accreditation as a sign that we are certifiably tested and up to the task of providing them with welding services.
The initial goal of the Nadcap audit was to ensure that there would be less of a need for primes to personally audit their suppliers, and in keeping with that, the audit has specialized, modified questions that can be asked of any supplier of a given prime. These portions of the audit are called supplemental checklists. This ensures that if a supplier is to keep their Nadcap accreditation, this is a trustworthy sign that they are up to their customer’s latest standards.
Likewise, if a company is to lose their Nadcap accreditation, then the prime will know that they are not providing a service that meets their compliance requirements.
In the welding industry, it therefore follows that a Nadcap accreditation is one of the base necessities for a supplier to have and maintain if they are to stay in business.
LYNN WELDING NADCAP FUSION WELDING SERVICES
A fusion weld is characterized by the merging of two or more materials – same or different – through the application of heat. The heat can come from a variety of means, such as gas/fuel, electricity, or laser beams. In some cases, filler material is added to the welding process and is melted down to bring about a homogeneous (as in the filler material is of the same composition/type as the base) or heterogenous (they differ in composition) weld. Not all fusion welding operations require or make use of filler material, but Lynn Welding has frequent need for them, so they are included in their Nadcap evaluation’s scope. Fusion welds that do not utilize filler material are referred to as autogenous.
To produce a fusion weld, the base materials have to be melted first and then, if applicable, the filler material should be allowed to melt and flow into the weld area. During this process, it is vital that the melting is fast but still under the welder’s control so that they can strictly monitor the weld pool forming. The welder must also have knowledge of heat affected zones (HAZ), as these too can negatively impact the integrity of the part if they are unaware or untrained in working/dealing with them. In addition, if there is too much heat generated, whether in a certain area or across multiple spots, then the part can become distorted as well.
To attain a Nadcap accreditation is to proclaim that your procedures and products are stringently maintained and measured to the highest of standards. To lose a Nadcap accreditation is therefore announcing the very opposite. Your customers will think you are sloppy, unreliable, and negligent in maintaining and managing your internal systems. There would be a significant loss to the business.
However, if we assume that the Task Group has approved the audit and corrective actions, then the company will be accredited as Nadcap approved to service the aerospace industry. This approval comes with the ability to use the Nadcap logo and name, which is likely to also attract more subscribers and customers into utilizing your business.
For Lynn Welding, this accreditation is especially vital for our business, because we provide services to the leading primes of the aerospace industry, as well as a number of military and defense ones. Our customers are especially reliant on our Nadcap accreditation as a sign that we are certifiably tested and up to the task of providing them with welding services.
The initial goal of the Nadcap audit was to ensure that there would be less of a need for primes to personally audit their suppliers, and in keeping with that, the audit has specialized, modified questions that can be asked of any supplier of a given prime. These portions of the audit are called supplemental checklists. This ensures that if a supplier is to keep their Nadcap accreditation, this is a trustworthy sign that they are up to their customer’s latest standards.
Welder & Inspection Qualifications
For every inspector and welder within the company, there must be proof that they are qualified for their position and their jobs. For both positions, the company must maintain and retain documentation proving that they have passed eye exams and weld and color vision testing. For resistance, welders have to have eye exams every two years and fusion is every year. The frequency of these tests also has to be explicitly stated in a written record. There must also be documentation covering who can and cannot work on certain materials/positions.
When qualifying a welder, the person and machine have to be qualified. There are two primary documents needed for the latter portion of the process: the weld production schedule (WPS) and the procedure qualification record (PQR). These ensure that our machines are capable of producing acceptable welds and that our schedules have been tested for consistency and repeatability. The PQR can be inspection certification, test result, or an old job qualifying the WPS, so long as it is objective evidence.
For inspectors, to prove that they are qualified for their position, the company has to have records in place showcasing that they have been tested and trained to aerospace standards. For Lynn Welding, we keep training records and eye exam results for all of our staff. This ensures that no one who is colorblind or not approved for a certain material – no one colorblind can work on titanium unless they test out of it (only applicable to some specifications, not all) – ends up working on or inspecting a job that they don’t have the qualifications for.
Material Cleanliness
In the aerospace industry, it is vital that materials are cleaned, maintained, and controlled. This is directly reflected in the fact that nearly every audit Lynn Welding has gone through has inspected for the control of cleanliness in relation to job or part materials. Nadcap checks to verify that there is a procedure in place for not only how staff should clean the materials but also for what needs to be done if any contamination occurs. They also check for how these procedures are flowed down to the floor.
In the case of Lynn Welding, the traveler that moves through the welding process with the job contains any relevant cleaning and packaging information from the customer’s or standard specifications. Some customers require their parts to move from stage to stage with very specific, protective measures. It is necessary then to have documented proof detailing how each staff member is trained to look for and identify those requirements. The same goes for cross-contamination records; a detailed training record goes a long way during an audit to ensure that all procedures, standards, and specifications are being followed and controlled for within a company.
Wire Brush
Since fusion welding often involves filler material and resources that need to be wire brushed, records need to be maintained that document the composition of the wire brushes used by the welders.
Additionally, all wire brushes should be controlled so that no welder can enter a booth, grab one of an unknown composition, and potentially contaminate a job. For this reason, the release, restocking, and labelling of the brushes are strictly accounted for at Lynn Welding and any unlabeled or untraceable materials are considered unusable.
Supplemental Checklists
There are such things as “supplemental” checklists. These specialized processes are ones that are specifically requested by the primes or subscribers that a company is recognized for servicing. For instance, Lynn Welding works on projects for Boeing, Bell Helicopter, Gulfstream, General Electric, Rolls Royce, and Raytheon, as well as a number of other primes, so the audit will often have an equal number of supplemental requirements to check over. The more primes the company works for, the more additional requirements – or supplemental checklists – that they will likely have to go through. Oftentimes, the prime’s checklists serve to double-check and verify that specific interests of theirs are properly reviewed and accounted for. Their checklists, just like those of the main audit, can change or alter paths.
Titanium: Some primes may wish to double check that lint free gloves are always required when dealing with titanium parts, especially if their projects routinely utilize titanium compositions.
The use of these gloves prevents stress corrosion. If the welds were to be touched directly, the chlorines would react with the residue left behind in such a way that causes stress corrosion cracking, which would result in the failure of that weld. Therefore, a subscriber who uses a lot of titanium may want to require that the use of gloves is properly regulated and controlled for in their suppliers. To document control for this, Lynn Welding has explicit directions on every job’s traveler and markings that travel with the parts throughout the welding process, as well as training records to attest to the competency of the staff who work with titanium.
Filler material: An OEM that uses very valuable or high-dollar material compositions may wish to confirm that all filler material used is strictly maintained. So, they may require the auditor to check how weld wires are stored, labelled, cleaned, and disposed of. A company such as Lynn Welding would then have to prove to the auditor that the weld wire is locked away, that only authorized personnel have access, and that the “authorized” person has the training or certifications necessary for that responsibility.
wire itself is of an appropriately assessed and documented composition. In this case, the quality team should have well-kept records documenting the certifications, proving the compositions and suppliers of their wires are reliably accounted for.
Gas: A prime who primarily relies on gas fusion welding may want to verify that their suppliers have a system in place that retains all certifications of conformance (CoC). The CoC may not be enough for them though so the certification of analysis (CoA), which costs a bit extra, and details exactly what is in the gas, may also be required by them. Again, these records should be maintained by the quality team and held onto for a time frame specified by either customer or standard specifications.
.png?width=300&name=Untitled%20design%20(75).png)
Lynn Welding Nadcap resistance welding services
A resistance weld forms when an electric current and pressure are used to join two materials. A resistance weld is a kind of fusion weld because the main component that works to fuse the joint together is the heat generated by the combination of electricity and force. The types of resistance welds that Lynn Welding specializes in are spot and seam.
A spot weld is a single point of welded material. It is often compared to a penny. The goal of this weld is to produce a nugget – the point where the pieces have been fused together – that has a low “corruption/pore defect” and high strength tolerance.
A seam weld is an overlapping line of spot welds. If the spot nugget is often compared to a penny, then a seam would be a line of pennies. These welds may also be required to pass non/destructive testing in order to qualify a machine or job process.
To test a nugget’s strength and ensure that they are up to customer standards, destructive testing is often done on coupons – sample sized pieces of the same composition – to determine the amount of force necessary to break the nugget. One such method is known as the pull test. The value provided by such methods are especially relevant for aerospace projects, as the moment that they will be under the most stress, and are most likely to fail, is when they are in the air. So, it is very important that this value is provided before moving forward with the job. To qualify a resistance machine’s weld schedule, it is necessary that twenty-five test coupons pass the destructive or non-destructive testing.
Similar to the fusion side of Lynn Welding’s capabilities, the audit for resistance welding is a thorough and detailed process. Therefore, this section will also only go over a few examples of what auditors may wish to review.
Machine Specifics
When a new machine is brought in, or a new job is being run on a different station, the welding schedule has to be verified for that machine. The records of the qualification therefore need to be verified and checked over during the audit. The machines at Lynn Welding store schedule data per part and job number, so the room for error is nearly non-existent when going from one job to the next on any one station. The audit will check to ensure, however, that the operators are verifying that the resistance schedule for the job being observed matches that of the one in use and that the machine itself can be trusted to produce accurate test results. The review of employees checking for the correct machine settings is also a means of evaluating a company’s internal flow down of information, and that they are actively training their staff to be competent and practiced in the verification processes to take place prior to beginning a job.
To qualify a schedule, the machine must pass a set amount of coupons of the same or similar composition of the job’s parent pieces. There should also be paperwork or documentation in place that proves the accuracy of the controller or time of the system. This can be a calibration record or some other pervasive record that can be made readily available to the auditor. The accurate measurement of time, as well as many other quantifiable processes, is essential to resistance welders.
When all of the afore mentioned aspects of the machine have been proven to be maintained and kept in as close to exact conditions from one month to the next, then the machine’s qualifying coupon tests will clearly be distinguished as an effectual means of proving that it is a reliable machine. The auditor will also likely check to ensure that the records detailing how these conditions are maintained, and their frequency as well, are readily available.
Acids
Our resistance department has an etching station that utilizes various acids and acidic compounds to test material. The Lynn Welding audit therefore verifies that we are properly monitoring the expiration dates for these acids. The quality system must also prove that the substances are controlled and certifiably evaluated to contain certain percentages of the chemicals necessary to fulfill their intended use. The documentation necessary for our etching station should then also show that the company we get our supplies from are legit and certified to standard. Due to the fact that different acids are used for different metals, the resistance department maintains accurate and detailed training records that fully prove that all variables involved within the process are controlled for through routine and thorough regimens.
Weld Nugget Inspection
When it comes to the inspection of weld nuggets, the auditor will often review that all of our procedures and documentation are compliant with Nadcap and customer specific standards. For the tests done to review/record the amount of penetration generated in one nugget, our forms should demonstrate that specific amounts tested, approved, and received are properly inputted. These forms should also chart a significant time span. Often, the quality system will state what system is in place to maintain the inspection procedures, how long it has been in effect, and where to find the forms to be filled out each time an inspection tool/fixture/resource is calibrated or tested in relation to said procedure.
Inspection Room
Similar to the weld nugget inspection procedure in place, the closed lab where our inspections for the resistance department take place must demonstrate that industry specific controls are in place. The routine maintenance of temperature, lighting and tooling calibrations, the labelling procedure of tooling and fixtures, and the clear and present designation of authorized personnel with access to sensitive or restricted material and valuables are just some among many controls that can be checked by a visiting PRI expert. All of which can be verified through the combined QMSF/QMSD files kept by the quality team and through walking the area themselves to check for any in-person failings that might be present. Since this particular point of failure would be especially catastrophic in the aerospace field, it is not uncommon for auditors to pay a great deal of attention and time towards their handling.
Resistance Weld Evaluation Test
If a facility has a resistance department, it will be necessary for one of their staff – typically the resistance engineer – to pass a test at the start of that specialty’s audit. The personnel involved are often able to choose what spec they will be using for the duration of the test, and then must examine and label diagrams of welds within that standard’s parameters. Often, the diagrams will ask the engineer to identify the specific penetration percentages and whether, based on the filled in variables, the nugget depicted would pass or fail. The people who sit for this test are often the ones placed in charge of qualifying weld nuggets regularly in the business, so if they were to score poorly or misinterpret a coupon, then it may be an indicator of a shortcoming or potential failing of the overall system.
Lynn Welding Nadcap brazing services
Unlike fusion and resistance, brazing does not melt the base material and instead is characterized by the melting of a filler metal that is then allowed to flow between the other pieces in order to join them together similarly to how a glue would. To properly create the right atmosphere for the direction and control of the weld area, flux is often used during the brazing process. The purpose of flux is to prevent the formation of oxide compounds, which can lead to complications in the braze area – such as porosity, discontinuous braze, and general poor quality. Like fusion welding, brazing can involve the use of gas and torches to create the heat needed to melt the filler material. The means of generating heat are widely varied for this process, so the amount of resources kept on hand, and therefore evaluated by the Nadcap audit, are relatively limitless. For this reason, only a handful of examples of what might come up during an audit have been provided for consideration in this section.
Brazing Certifications
Since there are a number of different necessary items involved in processing a brazing job, the idea of establishing a system to track the certifications for everything can seem daunting to new or developing companies. It is crucial, however, that a company retains the documentation necessary to establish their products and resources as certifiable and compliant with aerospace standards.
This means keeping the certifications and paperwork for all gas, filler wire, flux, and operator records. For every new item that comes into contact with a job, that directly impacts the end produce, there should be a paper trail for that item proving that it came from a reliable source, was controlled during its time in the building, and, if applicable, routinely evaluated as maintaining its accuracy.
Compliance to Specifications
To prove that brazing procedures are adhering to customer and standard specifications, there are a variety of sources that an audit proctor may choose to look at. Remaining fully compliant to a WPS is one of the base requirements of running a welding shop, but it is not unheard of for some businesses to fail even in the simple task of accurately recording the any NCR occurrences or routine reviews of the staff or follow up training records. These things are considered basic, standard practice at Lynn Welding. Routine review of the efficacy of our system is a key point in maintaining our merit status and drives our company to greater and greater innovative procedures. Maintaining and improving upon the foundations upon which any department works is the jumping off point of success.
Boiling Water Cleaning Tank
Lynn Welding uses boiling water cleaning tanks to clean brazed parts following the brazing process. In order to ensure that this portion of the procedure is functioning at optimal levels, as it should, there are controls in place, per Nadcap and customer specific standards, to verify that it is kept within excellent working condition. The training of the operators will firstly show – outside of viewing their work in person – that the educational background of the people in charge of these projects is certified for the task before them. Next, the auditor may look for the qualifying documents that ensure that the material and parts have been reliably tested and documented as effectively within tolerance to perform the cleaning process necessary. This entails evaluating the thermometers, the tanks and the fuel-source itself. A thermometer that has not been routinely calibrated will not read accurately and therefore presents the risk that the tank itself is not being prepared to standard. To qualify that the cleaning tanks and cleaning process works, a halide test can be performed, which will provide objective evidence to either support or reject the above methods.
Halide Testing
The term “halide” is the designation attributed to binary halogen compounds. Halogen compounds refers to a sub-group of elements with an extra valence electron – unbonded electron. So, a halide, in turn, refers to a halogen that has paired with a chemical that is less electronegative than itself – like fluoride or chloride. One half of the halide would be a halogen and the other would be a different chemical. A flux that contains fluoride and chloride must undergo a halide test according to the current Nadcap requirements. The flux is likely to only contain one halogen or the other, so it’s really only necessary to test for one or the other and seldom ever both. If there is no presence of halogens after performing a halide test, then the part has passed the cleaning stage and has successfully had all of its flux removed. In order to ensure that this test is as accurate as possible, the certifications and accreditations of the halide testing itself and the vendor that supplied it, if applicable, must be retained. Additionally, the expiration dates on these kits should also be strictly monitored and checked for.
Gas Control
Here at Lynn Welding, gases are commonly used for our brazing projects, so our audits routinely evaluate the upkeep and storage of our gas tanks. The companies providing the gas itself should have their own credentials and certifications kept on file, to verify that the source itself is of a verified quality. The gas tanks should be placed in a controlled, restricted area when not in use and unopened. Empty tanks should have a documented disposal procedure in place. Additionally, certifications of the gas itself, confirming conformance and analysis of the chemical compounds contained in the tanks, must be retained for a duration of time that complies with Nadcap and customer requirements.
.png?width=300&name=torch%20brazing%20(1).png)
Bibliography
Tell Us About Your Next NADCAP accredited Welding Project
To learn more about our NADCAP Welding capabilities and to receive a quote please submit a request below. All requests for quotes will be fulfilled within 24 business hours!